•3 layers
–Epoxy
–Adhesive
–Polyethylene
•Replication of mill-applied 3-layer PE coating
•Factory made design/system
Function of the intermediate adhesive
Maximise the adhesion to:
Polyethylene (Mechanical Protection) & Epoxy (Corrosion Protection)
Good shear resistance
Sleeves
–Epoxy
–Adhesive
–Polyethylene
Reconstructs mill-applied coating performance
Liquids
Sole adhesive to bond to 4 materials:
–Steel
–Epoxy
–Adhesive
Polyethylene
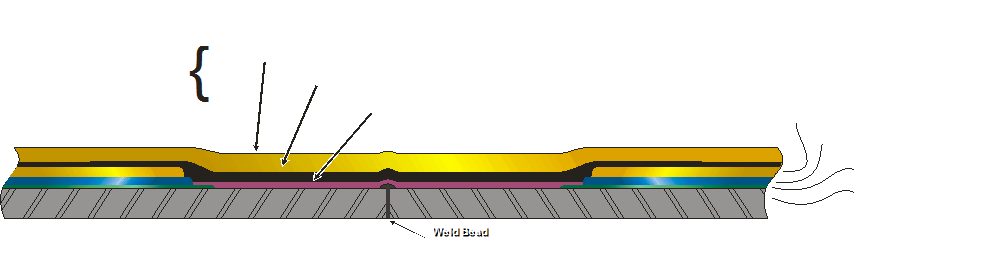
•Adhesion Epoxy-Metal: 20-30MPa (ISO = 10 MPa)
•Adhesion PU-Metal:10-15 MPa (ISO = 10MPa)
•Adhesion PU / Epoxy - PE
•Not compliant with ISO 21809-3
•Adhesion of Heat Shrinkable Sleeves on Steel is the same as Adhesion on PE
Line coating
determines the choice of girthweld protection.
Heat-Shrink
Sleeves
- PE 3 layers
- PP 3 layers
- FBE
- PU
Liquids (Epoxy/PU)
- FBE
- PU
Heat-shrink Sleeves
•Surface Preparation
•Pre-heating
•Mixing and application of Epoxy
•Sleeve Application
•Shrinking (Torch)
•Dielectric Testing (identical voltage)
(Irrelevant of the ambient conditions)
Liquids
•Applicator Protection (Spray)
•Prepare equipment (Spray)
•Surface preparation
•Pre-heating (especially PE)
•Appropriate mixing
•Roll or Spray
•Check and build up thickness (3 x 500 microns)
•Polymerization & Protection
•Dielectric Test (different voltages)
(Ambient Conditions RH < 80% to avoid Blistering)
Pinholes are a consequence of entrapped air and moisture
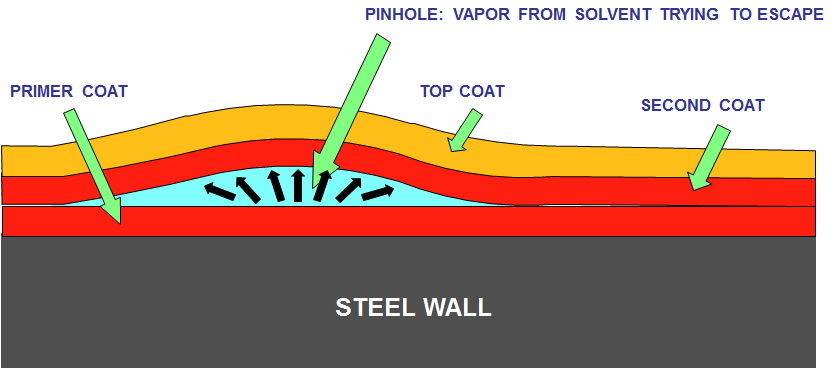
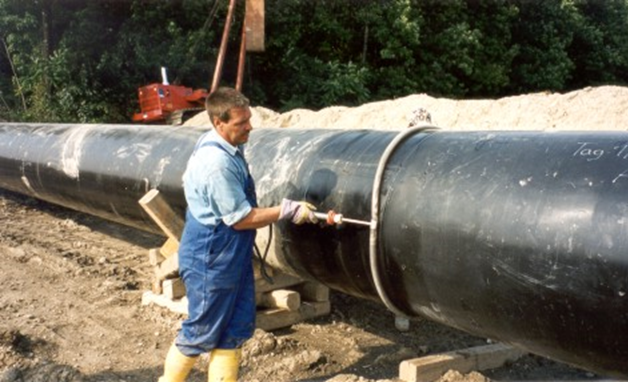
Welds / day (48”) : 50 - 170 (0,6 - 2km)
Sleeves
–Surface preparation (4-5min)
–Crew of 4 people
–6 joints / hour
–60 joints / day / crew
–1 crew for +/-50 joints
–3 crews for 170 joints
Easy logistics
Liquids
–Surface preparation (4-5min)
–3 passes (1500 microns)
–3 to 4 minutes coating interval
–10 to 15 minutes / joint
–40 joints / day / crew
–1 crew for +/-50 joints
–4 crews for 170 joints
Complex logistics
(Machine – product – storage – pot life)
Planning is driven by welding cycle time
Diameter: 48” – Cutback: 150mm
Sleeves
HTLP80 EN12608-UV
– Overlap: 50mm
– Thickness: 2,8 – 3 mm
– 100 / joint
Liquids
Epoxy Powercrete R60 & R95
–Overlap: 100mm
–Thickness: 1000-1500 microns
–Wastage: 50%
–5 liters (8kg) / joint
6-10US$/kg: 100-160 / joint
Polyurethane
–Overlap: 100mm
–Thickness: 1500 microns
–Wastage: 50%
–6 liters (9,6kg) / joint
5-6US$/kg: 100-120 / joint
- Superior system: Adhesion to PE
- Compliant with international standards
- Does not cause delays (preference of contractors)
- Comparable budgets
This solution ensures the longest service life
Diameter: 48” – Cutback: 150mm
50 – 55 US$ / joint
Liquids
Epoxy Powercrete R60 & R95
–Overlap: 100mm
–Thickness: 1000-1500 microns
–Wastage: 50%
–5 liters (8kg) / joint
6-10US$/kg: 48-80US$ / joint
Polyurethane
–Overlap: 100mm
–Thickness: 1500 microns
–Wastage: 50%
–6 liters (9,6kg) / joint
5-6US$/kg: 48-58 US$ / joint